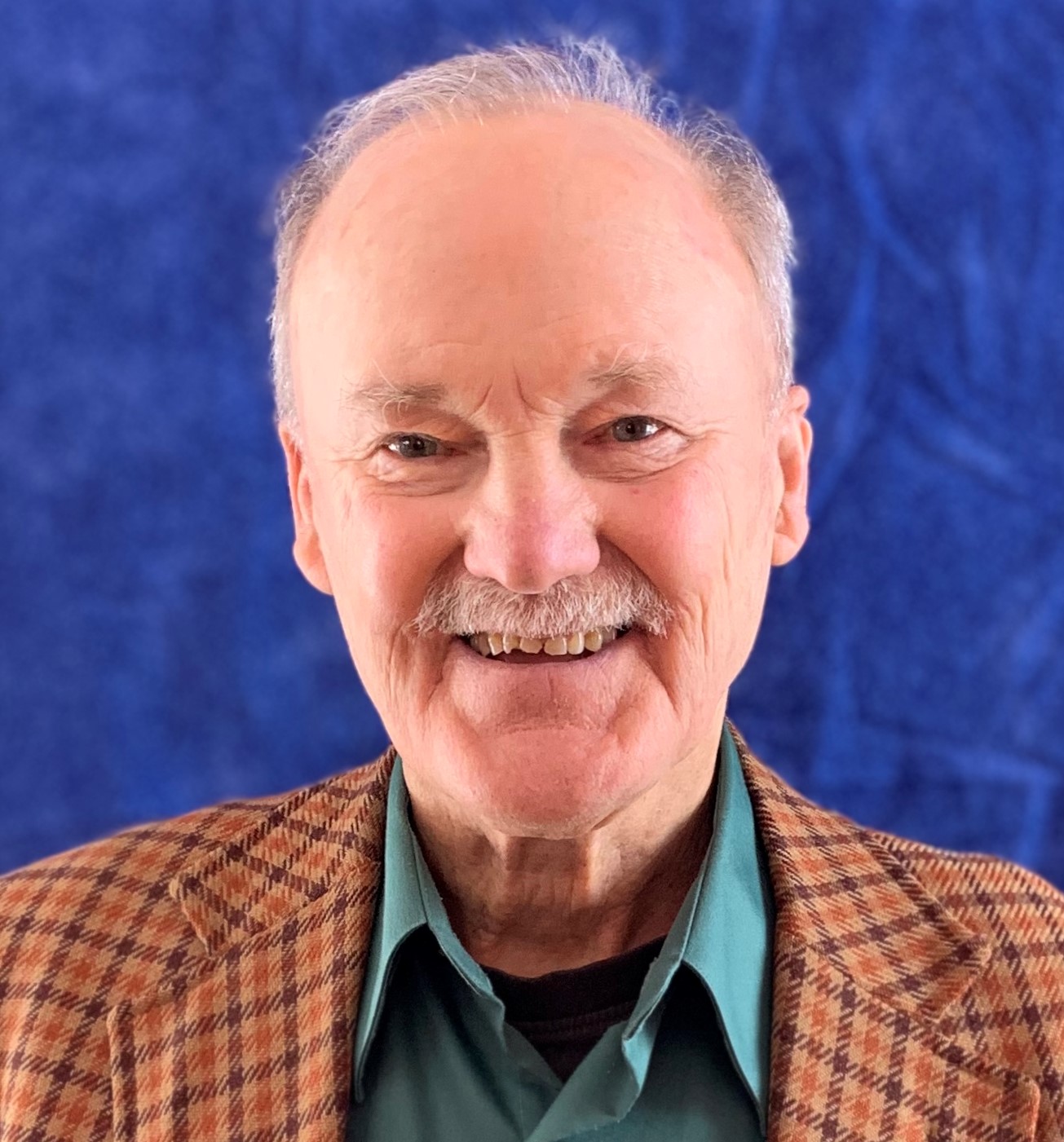
Harvard University │ Cambridge, Massachusetts
For outstanding contributions in the development of theories of the stability and failure of materials and structures, which have had profound impact on critical technologies for aerospace, energy systems, and nanoscale materials.
Think of an eggshell, a shape leveraged by nature for its efficiency in providing reasonable protection and structural integrity, and you can extrapolate why engineers in the aerospace, automotive, and energy sectors use shell structures to protect technology. Characterized by graceful curves and minimal thickness, they serve as the casings, hulls, and capsules for rockets, phones, fuel tanks, and more. However, the very qualities that make shells advantageous—thinness and curvature—render them vulnerable to buckling and instability. Engineer John Hutchinson has profoundly shaped our understanding of these vulnerabilities, particularly through his groundbreaking contributions to the study of shell buckling and its implications for rocketry and high-pressure vessels.
After earning his bachelor’s degree in engineering mechanics from Lehigh University, Hutchinson's pioneering work began during his graduate studies at Harvard, culminating in his Ph.D. in mechanical engineering in 1963. Early on, he identified critical gaps in classical theories of structural mechanics, which often overlooked the influence of small imperfections on the stability of shell structures.
His research was justified by the failure rate of rocket shells in the 1960s U.S. space program. Apollo engineers, ever conscious of weight, would design the shells of the Saturn V to the minimum thickness specified by material models of the time, only to witness the shells buckle from the crushing forces of the rocket's weight pushing down against the massive upward thrust of its engines. Adding to their frustration, the location of shell buckling would be inconsistent between tests, making spot-reinforcement impossible. This resulted in rocket shells being designed to be thicker and heavier than theoretically needed.
Knowing that traditional models assumed perfect geometries and uniform material properties, which rarely matched real-world conditions, mechanics experts as early as the mid-1940s began to realize that exceedingly small deviations in geometry or subtle variations in thickness could drastically decrease a shell’s load-bearing capacity, triggering unexpected and potentially catastrophic failures. Hutchinson’s contribution came from systematically investigating these imperfections and their outsized effects on structural stability. Through a blend of theoretical analysis and computational modeling, and comparison with empirical experimentation, Hutchinson demonstrated that shells of all types, not just rockets, could buckle under significantly lower stresses than classical theories predicted. He developed sophisticated mathematical models that accurately captured how minor, microscopic imperfections, introduced during manufacturing or otherwise, became amplified under stress, leading to catastrophic failure. The research influenced industry-wide shifts in design philosophies, leading directly to the adoption of rigorous inspection protocols and design standards, especially in critical industries like aerospace and energy, where safety and reliability are paramount.
Global space programs took notice. Prior to the research in which Hutchinson participated, rocket components were often over-engineered, leading to increased weight, reduced payload capacity, and inefficiencies. By precisely identifying how imperfections lead to buckling and failure, Hutchinson enabled aerospace engineers to optimize designs, making rockets lighter, more reliable, and capable of carrying heavier payloads into orbit and beyond.
Additionally, Hutchinson’s influential work in fracture mechanics complements his buckling research. Investigating crack propagation at microscopic scales, he uncovered critical insights into how damage initiates and spreads through structures, helping engineers understand how seemingly minor cracks could quickly lead to catastrophic failures. This understanding was critical for safety-critical structures such as offshore drilling platforms and pressurized vessels in chemical and energy industries.
Now the Abbott and James Lawrence Professor of Engineering at Harvard, Hutchinson has cemented his academic legacy in tangible outcomes, such as his mentorship of students who developed improved computational methods for predicting rocket shell buckling, directly impacting NASA’s rocket design protocols. His interdisciplinary collaborations have led to significant innovations, including integrating advanced finite element analysis with physical experiments to identify and rectify flaws in high-pressure fuel tanks before catastrophic failures could occur. Hutchinson’s team notably enhanced predictive modeling for automotive crashworthiness, allowing manufacturers to more accurately simulate collisions and reinforce vehicle structures effectively prior to physical testing.
In industry, Hutchinson’s research has directly influenced safety standards and manufacturing practices. Industries ranging from aerospace to automotive to energy have adopted his findings into their operational frameworks, implementing rigorous inspection protocols to identify imperfections early. This proactive stance significantly reduced failure rates in pressure vessels, pipelines, and critical aerospace components.
Hutchinson’s research over his 60-year career has been recognized with many honors, including medals from the American Society of Mechanical Engineers (ASME) and the American Society for Testing and Materials (ASTM). He is a member of the National Academy of Sciences, the National Academy of Engineering, and the American Academy of Arts and Sciences, as well as a fellow of ASME.
Today, John Hutchinson’s contributions remain central to ongoing innovations in structural engineering. By elucidating the subtle mechanics of structural stability and failure, Hutchinson has helped ensure the safety, efficiency, and reliability of essential structures upon which modern society depends. His career exemplifies how fundamental research can profoundly shape practical engineering, making even the most delicate shell structures robust enough to withstand the demanding conditions of contemporary industrial applications.
Information as of April 2025.